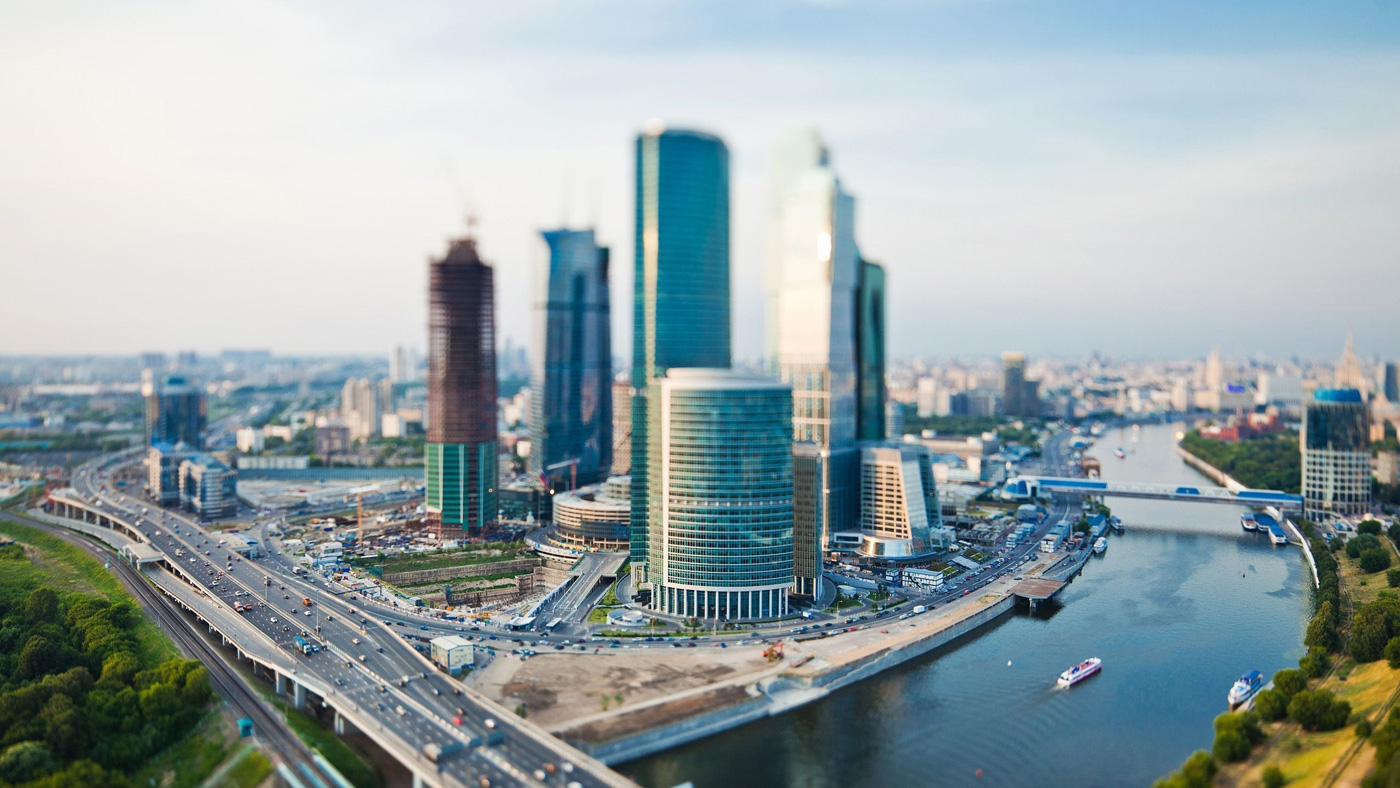
Удивительное дело, но вообще все забыли, что мы с вами живем в железном веке. И этот железный век, как бы ни говорили сейчас о новых материалах, которые придут на смену металлическим материалам, о новых принципах создания изделий, в ближайшее время еще никуда не денется.
Это тот редкий случай, когда промышленный запрос существует еще до того, как разработана технология. Мы работаем по прямому заказу отечественной промышленности, а именно «Объединенной двигателестроительной корпорации»...
Интересно, что, фактически, зародилась и эта, и другие технологии, разработанные Глебом Туричиным и его командой – из чувства обиды. За державу:
--- Все, что здесь есть, возникло потому, что мне захотелось увидеть в железе придуманное и просчитанное мною на бумаге. Захотелось 20 лет назад, когда меня одним из первых русских позвали в лазерные центры Германии. Я приехал, посмотрел, как все устроено, и меня охватило чувство обиды. Потому что уже тогда мы могли работать и работали не хуже их, но результат был иной.
Если вернуться к «промышленному запросу» и последствиям неожиданно быстрого для российских условий союза промышленности и науки, то заказанное Самарским заводом им.Кузнецова кольцо диаметром почти два метра, выращенное всего за 200 нормо-часов с машиностроительной точностью (в 15 раз быстрее, чем традиционным способом ), вызвало настоящий переполох в западном научно-техническом сообществе, считающем эту прогрессивную сферу исключительно своей монополией.
Реакция «монополистов» будет тем более понятна, если знать, когда и как команда Глеба Туричина начала по-настоящему заниматься аддитивными технологиями, а также, какими ресурсами она обладала на старте:
Работа по проекту ФЦП ИР "Создание технологии высокоскоростного изготовления деталей и компонентов авиационных двигателей методами гетерофазной порошковой металлургии" родилась из заказа Объединенной двигателестроительной корпорации, которая технически и организационно очень продвинута. Прослышав или вычитав где-то, что у нас есть задел по технологии прямого лазерного выращивания изделий, они приехали, посмотрели. Сформулировали нам ТЗ. Договорились, что ОАО "КУЗНЕЦОВ" при поддержке губернатора Самарской области Н.Меркушкина возьмется соинвестировать нашу работу. Обратились в Минобрнауки России, где объяснили, как это все стране нужно. Там нашли понимание. Был объявлен конкурс по мероприятию 1.4, то есть по проблемно-ориентированной тематике... Это первый раз такое было - нас "заставили" делать работу с нуля примерно за полгода до того, как был объявлен конкурс, и мы предложили проект. Исключительный случай для российской промышленности, когда сама корпорация "заточена" на поиск инноваций. Обычно надо "пробивать стенку лбом", а тут наоборот, тебя хватают, говорят: "Сделай, надо!"...
А начиналось все вот так:
--- Четыре года назад (в 2013 году) из наличного был ангар на улице Хлопина, 8а, и то, что недорого можно был купить в ближайшем магазине «Максидом» в виде шлангочков и трубочек. У нас была немецкая установка для сварки и термообработки, Там были лазер и робот. Мы эту установку модернизировали, приделали на нее другое сопло, поставили другой вращатель, научились правильно все нагибать и сыпать...
Ученый с рабочей грязью под ногтями
Вырастили круглую трубочку. Потом конусок. У нас была немецкая установка для сварки и термообработки. Там были лазер и робот. Мы их переделали. Мы пробовали вырастить что-то. Вот вырастили трубочку. Она сломалась в руках. Повозились месяц, научились вращать эту трубочку так, чтобы не ломалась и еще, чтобы раскрывался конусок.
А потом приехавшим товарищам мы сказали, что забесплатно дальше работать не будем. А это был Феликс Шамрай, - руководитель проекта в Объединенной двигателестроительной корпорации (ОДК). Он притащил сюда Дмитрия Колодяжного, который был заместителем директора ОДК по развитию. Мы сказали: изыщите нам денег, а мы сделаем настоящую технологию по выращиванию чего-то. Говорят: вт у нас такие большие авиационные двигатели, надо сделать такие. Мы говорим: Хорошо, утром деньги – вечером стулья. И в итоге они нам действительно очень здорово помогли.
Пока мы тут возились, я пытался понять, откуда вообще эти ограничения на толщину стенки, откуда влияние, или невлияние толщины слоя на механические свойства, есть ли анизотропия... Потом два года, уже понимая все эти вещи, мы этого никому не рассказывали. Рассказал я впервые на конференции в сентябре 2016 года. Тогда я опубликовал статью «К вопросу об устойчивости...», где было написано то условие математическое, которое нужно соблюсти, чтобы получить большую производительность. К этому моменту у нас уже были свои установки, не нужно было держать это знание в качестве конкурентного преимущества. И тогда мы сразу получили большой государственный проект, - деньги от Минобрнауки и Самарского завода им. Кузнецова, принадлежащего ОДК. По 112 миллионов рублей они сложились, чтобы мы построили установку.
Если бы не было этой государственной поддержки, ни черта не догнали бы [ иностранных коллег - shed ], потому что и так опоздали со стартом на несколько лет.
Что касается вещей запланированных, то с темпом в два года ( сказано 15 ноября 2015 года - shed ) выйдет большая отечественная машина для послойного выращивания из металлов, которая будет комбинировать разные материалы в ходе одного процесса. Эта разработка должна решить проблему производительности, ведь сейчас у прямого выращивания производительность очень высокая – порядка 20 кг/час. Это значит, что изделие весом в 500 килограмм можно вырастить всего за 25 часов. А послойные технологии производства, конечно, точнее прямых, но производительность у них гораздо ниже: производительность в 100 г/час – недостижимый предел. Поэтому многие разработки сейчас движутся именно в этом направлении – в сторону увеличения производительности нового типа машин. Кроме того, готовится к выпуску большая отечественная машина для прямого лазерного выращивания. Она, в общем-то, уже построена, только проходит так называемую опытную эксплуатацию.
О тонкостях сложения и вычитания металлов
Из лекции Глеба Туричина, прочитанной 8 апреля 2016 года:
Удивительное дело, но вообще все забыли, что мы с вами живем в железном веке. И этот железный век, как бы ни говорили сейчас о новых материалах, которые придут на смену металлическим материалам, о новых принципах создания изделий, в ближайшее время еще никуда не денется.
Длится этот железный век у нас с вами примерно последние 3500 лет, и за всё это время количество технологий обработки материала не увеличилось. Технологии менялись, но, как когда-то литейщики отливали наконечники стрел, так до сих пор такие технологии, как литье, очень широко используются в промышленности во всем мире. И эта промышленность сейчас построена в основном на технологиях литья и резанья. Сначала что-то отливается, потом это что-то режется, может быть, деформируется. Это так называемые технологии вычитания. Но, наверное, в последние 10–15 лет развивается новый комплекс технологий. Это не технологии вычитания, а это технологии сложения, или аддитивные технологии.
В отличие от технологий литья и резанья, аддитивное производство построено на добавлении материала. Изделия создаются за счет добавления металлического порошка, либо металлической проволоки, либо металлического расплава туда, куда нужно. И такой подход позволяет, с одной стороны, очень здорово экономить материал, а с другой стороны, совершенно революционным образом повышать производительность процессов. И то, что раньше делалось месяцами, сейчас может делаться за часы. И третье, что дают аддитивные технологии и что невозможно получить по-другому, — это возможность создавать изделия такой формы, которую никакие традиционные технологии принципиально создать не могли. То, что я сказал, сейчас, наверное, уже является общим местом, потому что аддитивные технологии на слуху в последние годы. Но от общих мест, от общих положений до конкретной реализации еще довольно далеко, и это обозначает путь, который можно пройти. Идти по этому пути интересно, и на этом пути тех, кто по нему пойдет, ждут не только приключения духа, но и интересные, опять же жизненные поражения и победы.
Сейчас основной из аддитивных технологий, использующихся человечеством, является технология послойного выращивания. Материал для этих технологий приготавливается в виде порошков. Потом из этих порошков создаются тонкие слои, в тонких слоях, там, где нужно, материал расплавляется либо просто нагревается, чтобы новый слой приплавился либо припекся к старому. Потом обработанный слой покрывается новым слоем порошка, и процесс повторяется. Так работают хорошо известные машины по технологиям SLS или SLM, и практически всё, что сейчас имеется в виду под аддитивными технологиями, относится к этим двум технологиям. И всё вроде бы неплохо. Действительно, таким образом можно выращивать изделия почти произвольной формы с очень высокой точностью, в реальности не уступающей точности механической обработки, из достаточно широкого спектра материалов. Но на пути реального промышленного применения встают две вещи. Вещь первая — это низкая производительность послойных технологий.
В реальности производительность машин для послойного выращивания ограничена десятками, редко — сотнями грамм в час. В принципе приемлемо, если, конечно, не нужно создать изделие весом 200 килограмм, например любимую нами среднюю опору газотурбинного двигателя. Тогда получается, что срок производства этой опоры по технологии послойного выращивания составит примерно 600 часов. Вряд ли кто-то способен выждать столько времени, и вряд ли можно обеспечить непрерывную работу технологической установки на протяжении 600 часов. Второй момент — то, что эта опора является изделием диаметром примерно два метра, таких послойных машин просто нет. Невозможно такую точную механику, которая нужна для этих послойных машин, в таком масштабе организовать. А вторая причина, которая является проблемной при внедрении аддитивных технологий, — это качество материала, которое при послойном выращивании получается. Дело в том, что эти порошинки, из которых состоит слой, довольно здорово ослабляют лазерное излучение, использующееся для оплавления порошка в слое, и получается так, что температура верхних порошинок и температура нижних различается. И если мы хотим с гарантией расплавить низ, то мы должны перегреть верх. А если мы не хотим вскипятить верх (а кипение на поверхности — это разбрызгивание и формирование дефектов), то мы низ должны недоплавить. В итоге у нас получаются поры.
Поры — это внутренне присущий всем послойным технологиям дефект. С ними можно бороться, их можно устранять последующим изостатическим прессованием — это когда изделие помещается на долгое время в горячую газовую камеру с очень высоким давлением. Поры таким образом медленно пластически залечиваются. Но технология крайне дорогая, а все-таки реальная промышленность состоит из двух вещей: наполовину, конечно, из техники, а наполовину из экономики, и всё должно быть дешевым. На фоне этих сложностей существует еще одна аддитивная технология.
Технология, которую мы называем прямым лазерным выращиванием, которая свободна от очень многих недостатков послойных технологий. Что это такое? Это технология, основанная на подаче порошка в зону выращивания с помощью газопорошковой струи, специальным образом сформированной в пространстве. Поток газа несет частички порошка. Этот поток газа должен быть правильно организован в пространстве, а плотность частичек порошка должна быть правильно организована внутри этой струи. Не так просто такую струю, которая нужна для выращивания, сделать. Но если такую струю сформировать и направить либо вдоль этой струи, либо под углом к ней сфокусированное лазерное излучение, то мы получаем возможность нагревать и частично оплавлять частички порошка в струе. Тогда, попадая на мишень, в ту зону, где выращивается изделие, эти частички сплавляются друг с другом, но почти от каждой частички остается одно маленькое твердое ядрышко, играющее крайне важную роль.
Дело в том, что эти нерасплавившиеся остатки порошинок становятся центрами новой кристаллизации. В таком случае кристаллизация расплава идет не от поверхности, на которой лежит расплав, а из объема. Объемная кристаллизация при прямом лазерном выращивании — это залог получения мелкозернистой структуры металла. А мелкозернистая структура металла позволяет получать механические свойства выращенных таким образом изделий практически на уровне проката или покова в зависимости от материала, чего никакие другие аддитивные технологии в реальности получить не позволяют, потому что послойная технология всё же обеспечивает структуру, близкую к структуре отливки или микроотливки. Это первый из больших плюсов технологии прямого выращивания. Почти нет проблем со структурой и свойствами выращиваемого материала.
Второй существенный момент — нет пространственных ограничений, потому что рабочим инструментом является технологическая головка, которая объединяет в себе две вещи: сопло для подачи газопорошковой струи и объектив, фокусирующий лазерное излучение. Но это небольшой и нетяжелый инструмент. Его можно дать, например, в руку роботу. И насколько хватит размаха у руки робота, настолько можно вырастить изделие (размах рук робота сейчас практически уже ничем не ограничен). Еще одно ограничение — это ограничение на внешнюю атмосферу. Всё же металл горячий, металл расплавленный. Хорошо бы защитить его от взаимодействия с активными газами. Но не существует больших проблем создать камеру, заполнить ее аргоном, и такие установки — робот с инструментом в руке, камера, заполненная аргоном, и система управления, — на мой взгляд, и являются сейчас самыми перспективными в аддитивных технологиях. Это уже даже не столько завтрашний день, сколько частично сегодняшний, они уже есть в металле. И третье, что для такой технологии замечательно, — она высокопроизводительна.
В реальности это скорости выращивания изделия, которые измеряются не в граммах в час, а в килограммах в час. Это значит, что тяжелое изделие можно сделать за смену-две...
А вот отрывки из беседы с Туричиным журналиста в помещении («габаритами, оснащением, скрежетом, визгом и грохотом схожим с заводским цехом») ИЛиСТ СПбПУ - Института лазерных и сварочных технологий Санкт-Петербургского политехнического университета Петра Великого – директором которого Глеб Туричин и является (с 8 ноября 2016 года, кстати, он назначен еще и и.о. ректора «Корабелки» - СПбГМТУ):
- Так вот, все, что здесь стоит на показ, - продолжает Глеб Андреевич, - не отлито, не отштамповано, а выращено. Это, например, корпус камеры сгорания. Раньше его неделю делали путем вальцовки и механической обработки. Мы растим этот корпус за три часа. Производительность в 100 раз выше той, что есть сейчас. На Международной выставке "ИННОПРОМ", что в июле [2015 года - shed ] прошла в Екатеринбурге, мы демонстрировали примеры изделий, полученных прямым лазерным выращиванием. Скажете, кто сегодня только не занимается аддитивными технологиями? Согласен. Многие уже умеют растить изделие со скоростью 150 граммов массы в час, а у нас - килограммы за то же время. Плюс все, что выстраивается лазером послойно, получается пористым. Для упрочнения надо деталь помещать в газостат и под высоким давлением при высокой температуре долго ее прессовать. Эта операция очень дорогая. А у нас сплошность получается сразу 100 процентов.
"Фишка" заключена в фундаментальной физике движения двухфазных потоков при переносе порошка газовой струей. В ИЛиСТ научились организовывать достаточно длинные ламинарные участки газовых струй, которые несут порошок, и умеют хорошо управлять его переносом и плавлением. Да так, что материал частично наследует структуру и свойства порошка, из которого выращивают изделие. Например, если порошок, из которого выращивают деталь, имел размер субструктурного блока 50 нанометров, то по окончании выращивания и кристаллизации получают размер блоков 100 нанометров. Крупнее вдвое, но, судя по испытаниям, механические свойства полученных изделий - на уровне проката. И таким путем можно делать реально большие вещи, скажем опоры авиационных двигателей, блиски - диски с лопатками. Причем если обычно на изготовление прототипа нового двигателя уходят годы, то при использовании новой технологии это удастся сделать в 100 раз быстрее. Вот это и есть настоящее импортозамещение...
Созданием подобных технологий занимаются и другие компании — американская Optomec, французская BeAM Machines, немецко-японский концерн DMG-Mori. «Мы видим, что есть нечто похожее — это общее движение, и наивно было бы полагать, что мы одни такие умные во всём мире. Во всяком случае, мы не отстали. Скорее, даже впереди...
- В чем эффективность вашей машины, - спрашивает Туричина журналист.
--- В эти наши машины заложены две важные вещи: устойчивость выращивания и бешеная производительность. Мы сейчас очень сильно превосходим всех по производительности.
- Всех ?
--- Всех. С точки зрения выращивания по технологии, которая использует порошок. Есть еще крайне интересная технология, где используется проволока. Мы тоже в этом направлении работаем. Вот когда наработаем и ускачем настолько вперед, что не будем бояться, тогда покажем.
А еще мы варить можем
- Мы - крупнейший в России центр в области промышленных лазерных и сварочных технологий, сравнимый по объему выполняемых прикладных работ с крупными технологическими центрами Германии. Но это не значит, что мы не занимаемся фундаментальной наукой. Просто у нас здесь все поставлено с головы на ноги. То есть сделано так, как должно быть. Потому что наука начинается с потребностей промышленности. Наука не бывает неприкладной, хотя может быть глубокой, фундаментальной, абсолютно теоретической...
--- ... признаюсь, для меня до сих пор объявить потенциальному заказчику цену - преодолеть барьер. Заставляют две вещи: чувство ответственности за тех, кто у нас работает, - они должны получать зарплату, и понимание того, что надо эту зарплату держать на уровне европейских институтов, а то переманят. Головы у нас не хуже, а потому велик шанс, что конкурентоспособный человек уйдет.
- Хотите сказать, что у вас люди получают под 200 тысяч рублей в месяц?
--- Сейчас, после кризиса (разговор происходит в августе 2015 года - shed ), меньше. И рискую, если за год не верну зарплаты на достойный уровень, начать терять кадры. При всей их лояльности, выносливости и терпении. У нас работают 32 человека, больше половины - моложе 35 лет. Им детей поднимать надо, жилье покупать.
- А за счет чего намерены выбраться из кризиса?
--- За счет того, что, живя в очень конкурентной среде, мы - лучшие: за последние годы разработали три технологии, которые в мире не имеют аналогов. Базируются на результатах наших же фундаментальных исследований, но придуманы потому, что эти технологии промышленности очень нужны.
Например, лазерно-дуговая сварка металлов больших толщин. Иногда надо сваривать тяжелые, толстостенные конструкции, да так, чтобы от термических напряжений в районе шва конструкция не потеряла форму. Вот, к примеру, судокорпусная секция из стали 20 мм толщиной. Если металл "поведет", конструкцию не выправить, а значит, и корабля нормальным образом не собрать. Фундаментальная суть процесса - сварка одновременным воздействием лазерного луча и электрической дуги. Причем лазерный луч играет роль управляющего агента для электрической дуги и обеспечивает сжатие дуги в точку, в пятнышко диаметром 1,5 мм. А мощность дуги около 15 кВт, и у лазерного излучения примерно такая же. Год назад эту гибридную технологию мы первыми в мире сертифицировали для судостроения. И сегодня самая большая в мире гибридная сварочная машина построена не за рубежом, а нами, специалистами СПбПУ Петра Великого совместно с Центром технологии судостроения на Северной верфи Санкт-Петербурга. Вот на стенде фотография этой гигантской конструкции: 14-метровый портал, рабочий ход - 12 метров. Сейчас машину отправили в Архангельск на завод "Красная кузница".
А вот в витрине то, чего ни у кого больше нет: примеры лазерной сварки разнородных соединений. Тех, которые "вообще не варятся". А мы умеем. Возьмем, к примеру, медь и алюминий. Когда пытаются их соединить обычным образом, возникают хрупкие промежуточные фазы и шов "разваливается". А в электромобилях, например в батареях, нужно соединять внутреннюю проводку с клеммами. Это был заказ "Самсунга", и мы его выполнили. Начнут наши делать электромобиль - тоже заинтересуются. Здесь заложена очень интересная физика, построенная на базовой теории - кинетике гетерогенных химических реакций с диффузией. Режимы сварки подбирали по результатам металлографических исследований. Хитрость состоит в очень кратком пребывании металлов в зоне высоких температур. Буквально мгновения, чтобы диффузия не успела сдвинуть атомы и "слепить" сплошную интерметаллидную прослойку. Сваривали разные металлы. Вот пара титан и алюминий - для соединения холодных и горячих трубопроводов в авиационных двигателях... Дальше в рядок лежат образцы титан-нержавейка, алюминий-бронза, сталь-медь, что используется в форсунках ракетных двигателей.